An Overview of Sucralose: Characteristics, Applications, and Synthesis Techniques
Introduction Sucralose, also known as trichloro sucrose, is a novel sweetener widely used in the food and pharmaceutical industries. Compared to other sweeteners like aspartame, sucralose has a taste closest to sucrose, with a sweetness 600 times that of sucrose and lower calorie content, making it a promising candidate for further development. As market demand continues to grow, large-scale production of sucralose is necessary. To achieve low-cost, environmentally friendly production, research on sucralose synthesis techniques and production management must be strengthened, paving the way for broader applications of sucralose.
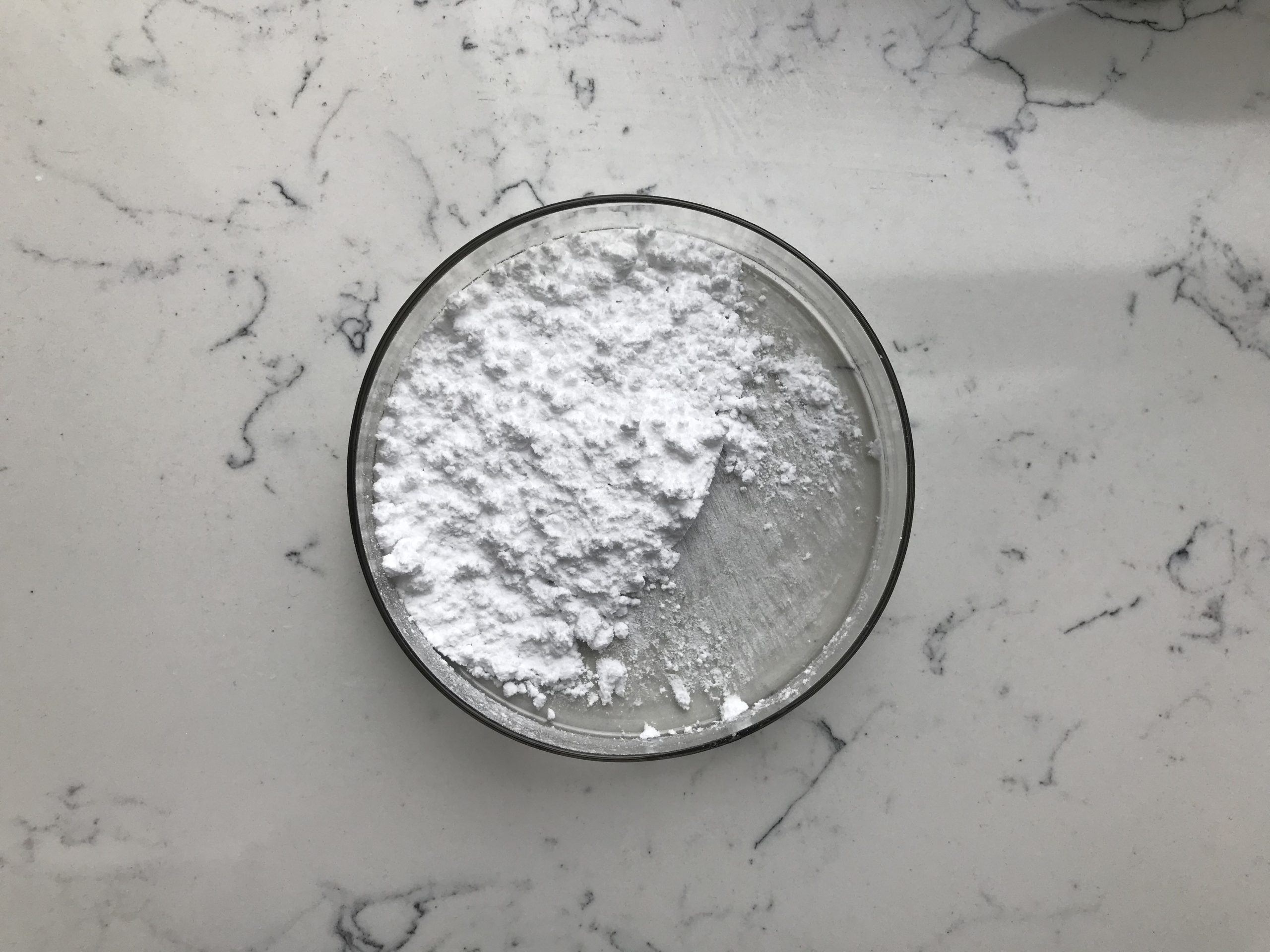
1. Characteristics and Applications of Sucralose
Sucralose, a chlorinated derivative of sucrose, closely resembles the taste of sucrose and significantly reduces sugar intake when used as a sweetener. Since sucralose is not absorbed by the human body, it has zero calories and is non-toxic with no side effects. Even at high temperatures, sucralose dissolved in water maintains its sweetness and stability, and does not undergo chemical reactions when combined with proteins and pectin in food during baking. Due to its pure sweetness and inability to be utilized by bacteria, sucralose is widely used in the production of various foods, such as jelly, ice cream, and chewing gum, as well as in pharmaceutical applications. However, challenges in sucralose synthesis, such as high production costs and environmental pollution from waste materials, must be addressed through further research to expand its application range.
2. Analysis of Sucralose Synthesis Techniques
2.1 Group Protection
Whether using chemical or enzymatic methods, the synthesis of sucralose requires deprotection and chlorination processes. Sucralose synthesis involves the substitution of different hydroxyl groups on the sucrose molecule with chlorine atoms, resulting in varying sweetness effects. Group protection involves protecting hydroxyl groups, followed by chlorination reactions, and finally removing the protecting groups to obtain sucralose. Various methods have been explored to improve the efficiency and yield of sucralose synthesis, such as the use of pyridine as a solvent to enhance hydroxyl group protection and the use of acetic anhydride for protection[1].
2.2 Monoester Method
The monoester method for sucralose synthesis involves esterification protection, selective reactions, and the removal of ester groups to obtain the final product. Different methods for preparing the key intermediate, sucrose-6-monoester, have been explored, including direct esterification, original acetic acid trimethyl esterification, and dibutyltin oxide method[2]. Each method has its advantages and disadvantages in terms of simplicity, reaction conditions, and raw material costs, with some methods being more suitable for industrial production.
2.3 Derivative Chlorination
Chlorination of sucrose derivatives involves the substitution of hydroxyl groups with chlorine atoms. The choice of chlorinating agents, such as sulfuryl chloride and pyridine, is crucial for ensuring efficient reactions and high-purity products[3]. New chlorination reagents and methods, such as the use of phase-transfer catalysts, are being researched to improve product yields, but industrialization has not yet been achieved.
2.4 Enzymatic Catalysis
Enzymatic catalysis can also be used for sucralose synthesis, with enzymes such as lipases and proteases exhibiting regioselectivity in acylation reactions and deacylation processes. Enzymatic catalysis offers advantages in fine chemical production, including reduced chemical reagent usage, mild reaction conditions, lower equipment requirements, and minimal environmental pollution. However, factors such as enzyme storage and screening limit the cost-effectiveness of this method for industrial production in the short term.In conclusion, sucralose is a promising sweetener with a wide range of applications in the food and pharmaceutical industries. Various synthesis techniques have been explored to improve the efficiency, yield, and environmental impact of sucralose production. Continued research and development in this field will help address the challenges and expand the application range of sucralose.
Exploring the Production Management of Sucralose
3.1 Production Process Management
The synthesis of sucralose is mainly achieved through the cost-effective and simple monoester method in industrial production. This method has been thoroughly studied, and the process conditions are relatively mature. In practice, the production process involves reacting recrystallized sucralose-6-acetate with CH3OH or CH30Na, followed by alcoholysis and resin neutralization. After filtration and distillation, activated carbon and water are added for decolorization. Further filtration and distillation lead to product crystallization, and ethyl acetate is added for recrystallization. Finally, the product is obtained with high purity after filtration and drying1.To ensure product quality, it is essential to strengthen process control, clarify responsibilities and management objectives for each position, and maintain stable operation of the production line. To reduce production costs, emulsified coke slurry can be introduced as an alternative to heavy oil, which can lower fuel costs and harmful substance concentrations in flue gas emissions. This also enables the secondary use of steam, further reducing production costs. During the chlorination process, it is crucial to control reaction temperature and time, such as maintaining the ambient temperature between 10 and 15℃ to increase product yield.
3.2 Production Equipment Management
In the production of sucralose, it is necessary to manage various equipment, such as reaction tanks, vacuum equipment, and concentration equipment, to ensure efficient operation and reduced production costs. Establishing an advanced maintenance management system and conducting regular inspections can help identify and address potential equipment issues, ensuring smooth operation and preventing major accidents.Daily management should focus on the specific characteristics of each equipment and strictly control operating parameters. For example, reaction tanks are mainly used for mixing raw materials and solvents and are sensitive to temperature changes. Rapid environmental temperature changes can cause stress concentration issues. Therefore, a strict management system should be established to ensure personnel perform slow heating or cooling operations. Clear safety production responsibility systems should be established based on equipment management objectives, and equipment operation manuals should be compiled according to positions. Regular personnel training, on-site operation guidance, and apprenticeship training methods should be implemented to ensure that personnel can operate equipment only after passing the qualification assessment.
3.3 Production Waste Management
The synthesis of sucralose generates a large amount of waste gas, which needs to be treated using different methods, such as chemical absorption. Considering the characteristics of gases like hydrogen chloride and sulfur dioxide, dispersed absorption devices are usually equipped for tail gas treatment in production. After chemical separation, gases like sulfur dioxide can be obtained, which can be condensed, enriched, and liquefied to produce by-products. The co-production method can convert sulfur dioxide into sulfuryl chloride, which can be further used in production.In cases where the production process is lengthy and involves multiple solvents and raw materials, the recycling and reuse of various organic solvents can not only reduce production costs but also decrease pollutant emissions. The wastewater generated during sucralose production typically contains a large amount of DMF (dimethylformamide), which can cause severe environmental pollution if discharged directly. To reduce the DMF content in wastewater, distillation separation can be implemented, leveraging the boiling point difference between water and DMF, with a recovery rate of around 96%. Additionally, dimethylamine treatment technology and biological methods can be used for DMF treatment, with the former enabling DMF recovery and the latter reducing wastewater treatment costs. In terms of solid waste treatment, activated carbon and other materials can be used to mix various carbonates and salts, producing products like compound fertilizers.