Polyglutamic Acid (PGA) is a biopolymer made up of glutamic acid monomers linked by peptide bonds. It has various applications, including in the food industry, medicine, cosmetics, and agriculture, owing to its biocompatibility and biodegradability. The production process of Polyglutamic acid can be achieved through two main methods: biosynthesis (fermentation) and chemical synthesis.
1. Biosynthesis (Fermentation Process)
- The majority of commercially produced Polyglutamic acid is obtained through microbial fermentation because this method is more environmentally friendly and scalable. Here’s an outline of the biosynthetic process:
A.Microorganisms Used
- Polyglutamic acid is typically produced by certain strains of bacteria such as Bacillus subtilis, Bacillus licheniformis, and Bacillus amyloliquefaciens. These microorganisms naturally produce PGA under certain conditions.
- Some other microorganisms, including Streptococcus thermophilus, can also be engineered to produce Polyglutamic acid.
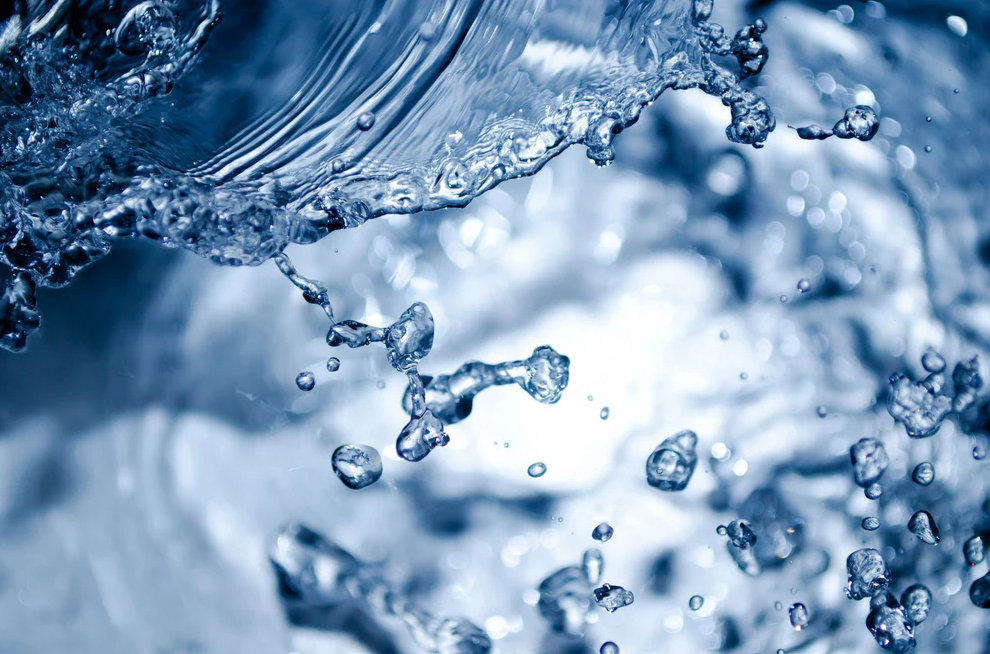
B.Fermentation Process
1.Culture Medium Preparation:
- A nutrient-rich medium is prepared, usually containing sources of carbon (e.g., glucose, sucrose), nitrogen (e.g., ammonium salts, amino acids), and other trace elements that facilitate bacterial growth.
- The pH, temperature, and oxygen levels are controlled during fermentation to optimize Polyglutamic acid production.
2.Inoculation and Fermentation:
- The selected strain of bacteria is inoculated into the culture medium. The bacteria start growing and synthesizing Polyglutamic acid.
- During fermentation, bacteria convert glutamic acid (which can be derived from glutamate salts or obtained by hydrolyzing proteins) into polyglutamic acid.
3.Control Conditions:
- pH control: The pH of the fermentation broth is monitored and adjusted (often between 7-8) to maintain optimal microbial growth and Polyglutamic acid production.
- Temperature control: The temperature is typically maintained between 30-37°C, depending on the specific strain.
- Oxygen supply: Aerobic conditions are required to promote the growth of the microorganisms, so aeration and agitation are important.
4.Polyglutamic acid Production:
- The bacteria secrete Polyglutamic acid into the fermentation broth as they grow. The production rate of Polyglutamic acid can vary based on the strain and fermentation conditions.
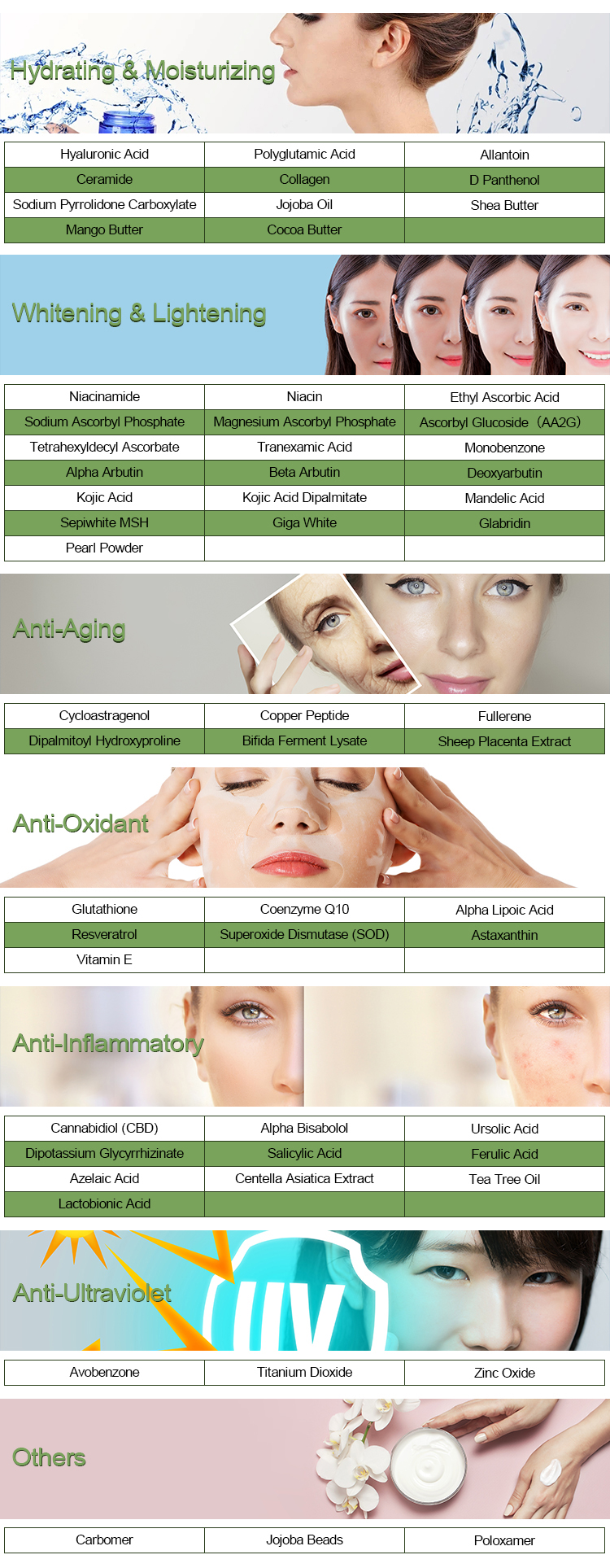
C.Harvesting and Purification
- Separation: Once the fermentation reaches the desired level of Polyglutamic acid production, the broth is harvested. The solid biomass is separated from the liquid by centrifugation or filtration.
- Polyglutamic acid Recovery: The polyglutamic acid is then extracted from the liquid phase, typically through methods such as precipitation with ethanol, filtration, or ultrafiltration.
- Purification: The crude Polyglutamic acid extract is purified by processes like dialysis, ion-exchange chromatography, or other techniques to remove impurities and by-products. The purified Polyglutamic acid is then dried and processed into the desired form (e.g., powder or gel).
D. Applications
- Polyglutamic acid produced via fermentation can be used in a variety of applications such as food additives, biodegradable packaging, cosmetics, and pharmaceutical formulations.
2. Chemical Synthesis of Polyglutamic Acid
Chemical synthesis of Polyglutamic acid involves the polymerization of glutamic acid or its derivatives in a controlled environment. However, this method is less common than fermentation due to its complexity and the potential for lower yields. Here’s a general outline of the chemical synthesis process:
A. Polymerization
- Glutamic acid derivatives like N-carboxyanhydride (NCA) of glutamic acid are used as monomers.
- A polymerization catalyst (typically a base like sodium or potassium hydroxide) is used to initiate the polymerization of the NCA monomer into Polyglutamic acid.
- The reaction is conducted in a solvent, and the polymerization can be controlled by adjusting the temperature and concentration of the monomer.
B. Post-Synthesis Processing
- Once the polymerization is complete, the Polyglutamic acid is separated and purified, typically using methods like precipitation or dialysis.
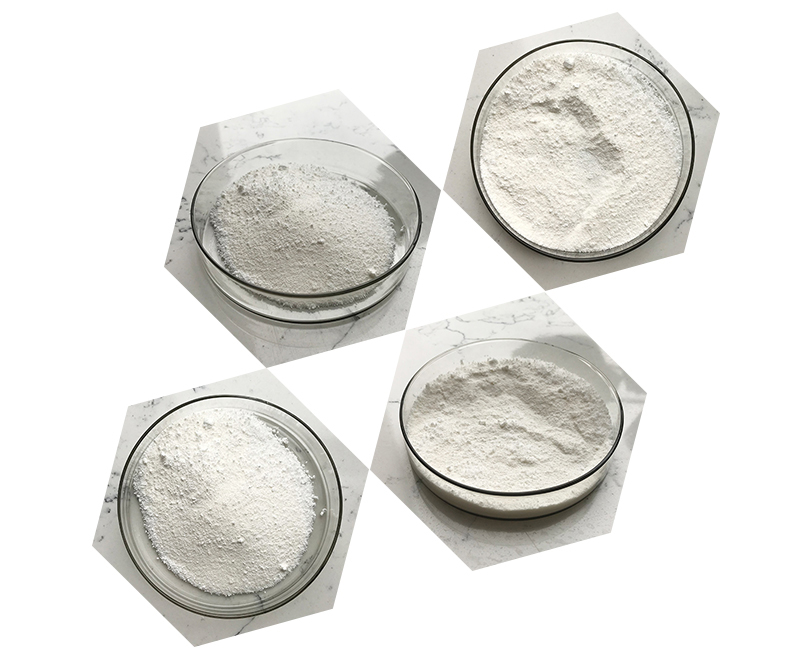
3. Key Factors Affecting Polyglutamic Acid Production
- Strain selection: Different microbial strains can produce varying amounts and types of Polyglutamic acid. Genetic modifications can improve yields.
- Substrate selection: The carbon and nitrogen sources used in fermentation impact the yield and quality of Polyglutamic acid.
- Fermentation conditions: Parameters like pH, temperature, and aeration must be optimized for maximum Polyglutamic acid production.
- Recovery methods: The efficiency of the extraction and purification methods plays a key role in the cost-effectiveness of production.
Conclusion
Polyglutamic acid is primarily produced through microbial fermentation, using strains of bacteria like Bacillus species. This method is cost-effective, environmentally friendly, and scalable, making it the preferred choice for commercial production. Chemical synthesis methods are more complex and less common.