Silk fibroin is a protein derived from the silk of silkworms, primarily Bombyx mori. It has gained significant attention in various fields, such as tissue engineering, biomedicine, and material science, due to its biocompatibility, biodegradability, and mechanical properties. Here’s an overview of the quality and production of silk fibroin:
1. Silk Fibroin Structure and Properties
Silk fibroin consists of two main components: fibroin (the insoluble protein) and sericin (a water-soluble protein). The quality of silk fibroin is largely determined by the fibroin component, which forms a crystalline, fibrous structure that gives silk its strength and resilience. Key properties include:
- Mechanical Strength: Silk fibroin has excellent tensile strength and flexibility, making it useful in applications requiring durability.
- Biocompatibility: It is highly biocompatible and non-toxic, which is why it is widely used in medical applications.
- Biodegradability: It degrades naturally over time, making it an eco-friendly material for various applications.
- Structural Integrity: Silk fibroin has a beta-sheet-rich structure that contributes to its rigidity and stability.
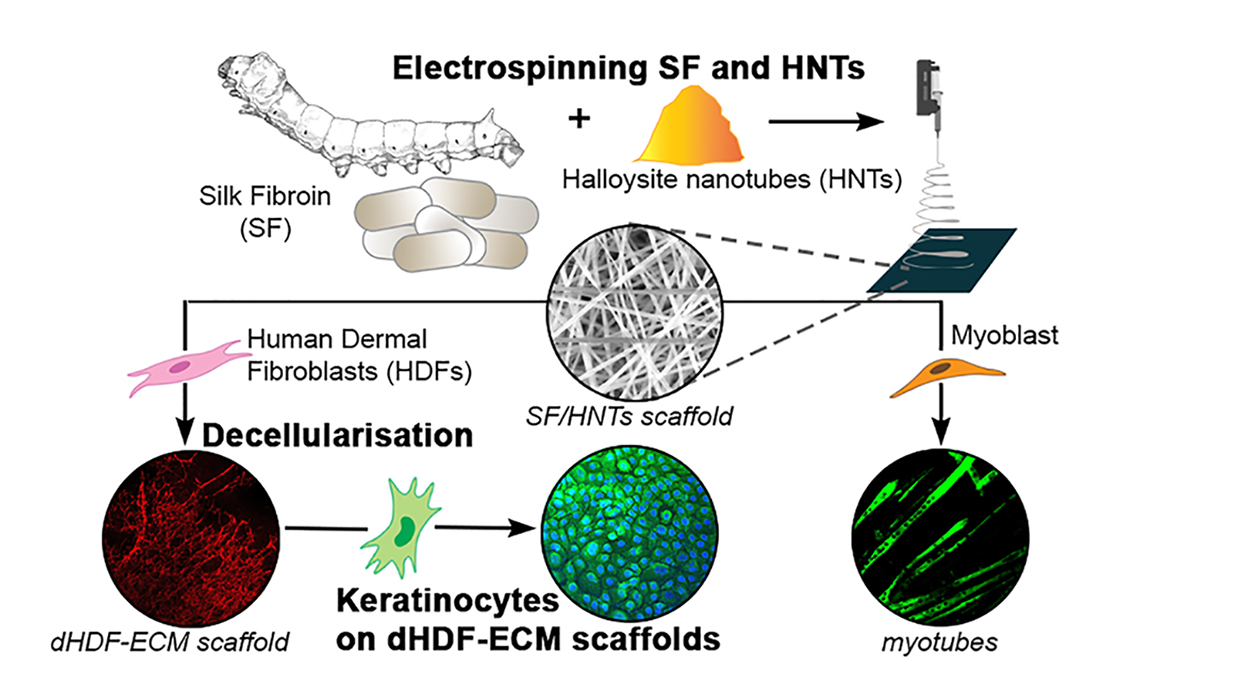
2. Silk Fibroin Production
Silk fibroin is primarily extracted from the silkworm’s cocoon. The production process generally involves several key steps:
a) Silk Production by Silkworms
Sericulture: Silkworms are raised in controlled environments where they spin silk threads to form their cocoons. The larvae of the silkworm produce two proteins: fibroin and sericin, with fibroin forming the structural part of the silk fiber.
b) Harvesting the Silk
Cocoon Harvesting: The silkworms are allowed to spin their cocoons for about 2-3 days.
Boiling to Remove Sericin: The cocoons are boiled or treated with hot water or alkaline solutions to remove the sericin, leaving behind the fibroin. This is crucial because sericin is water-soluble and must be removed for further processing.
c) Silk Fibroin Extraction and Processing
Dissolution in Ionic Liquids or Organic Solvents: To extract pure silk fibroin, the sericin-free fibers are often dissolved in solvents such as lithium bromide or calcium chloride solutions. This process may involve using specific ionic liquids to ensure that the fibroin is not denatured during extraction.
Dialysis and Purification: The dissolved fibroin solution undergoes dialysis to remove excess salts or chemicals, yielding a purified fibroin solution. The purity of the fibroin affects the quality of the final product.
d) Regeneration and Processing
Film, Gel, or Fiber Formation: Once the fibroin solution is obtained, it can be processed into various forms like films, gels, or fibers. This is done by:
Drying: To form silk fibroin films.
- Spinning: To form fibers for textile or medical applications.
- Gelation: In tissue engineering or drug delivery systems.
- Crosslinking: Sometimes, the silk fibroin is crosslinked chemically or physically to improve its mechanical properties or enhance its stability in certain applications.
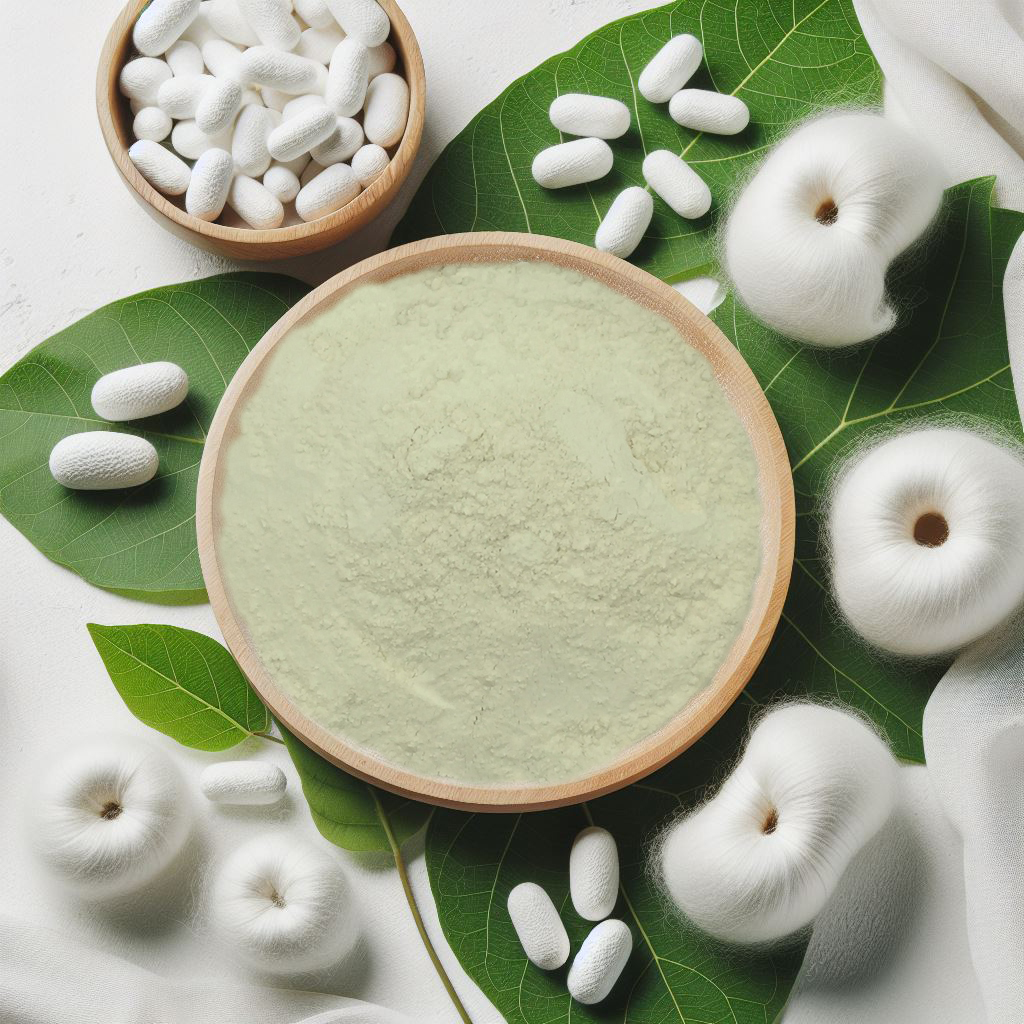
3. Quality Control of Silk Fibroin
The quality of silk fibroin is critical, especially for medical and industrial uses. Key factors influencing quality include:
- Purity: The absence of sericin and other impurities is essential for many applications.
- Molecular Weight: The molecular weight of silk fibroin affects its mechanical properties and biocompatibility. Typically, higher molecular weight fibroin has better strength and stability.
- Structural Integrity: The beta-sheet content (which is responsible for the crystallinity of silk fibroin) needs to be preserved. Overprocessing can lead to degradation and loss of these properties.
- Mechanical Properties: For biomedical uses, such as scaffolds, the tensile strength, elasticity, and degradation rate must be finely tuned.
4. Applications of Silk Fibroin
- Biomedical Applications: Silk fibroin is used in drug delivery systems, wound dressings, tissue engineering scaffolds, and as a biomaterial for various medical devices. Its ability to form a gel-like structure makes it ideal for controlled drug release.
- Textiles: Silk fibroin has been used in high-quality textiles due to its softness and luster.
- Biodegradable Plastics: As a biodegradable polymer, it’s being explored for use in sustainable packaging and other environmentally friendly materials.
- Nano- and Microfabrication: Due to its controllable properties, silk fibroin is also used in creating nanoparticles and microspheres for drug encapsulation or delivery.
5. Challenges in Silk Fibroin Production
- Cost and Scalability: The production of silk fibroin remains relatively expensive, particularly because of the labor-intensive nature of sericulture.
- Environmental Conditions: Silkworms are sensitive to environmental conditions, and changes in temperature, humidity, or diet can affect the quality of silk produced.
- Processing Variability: The quality of the final fibroin product can vary depending on the methods used for extraction, which can lead to inconsistencies in properties such as mechanical strength, biodegradability, and bioactivity.
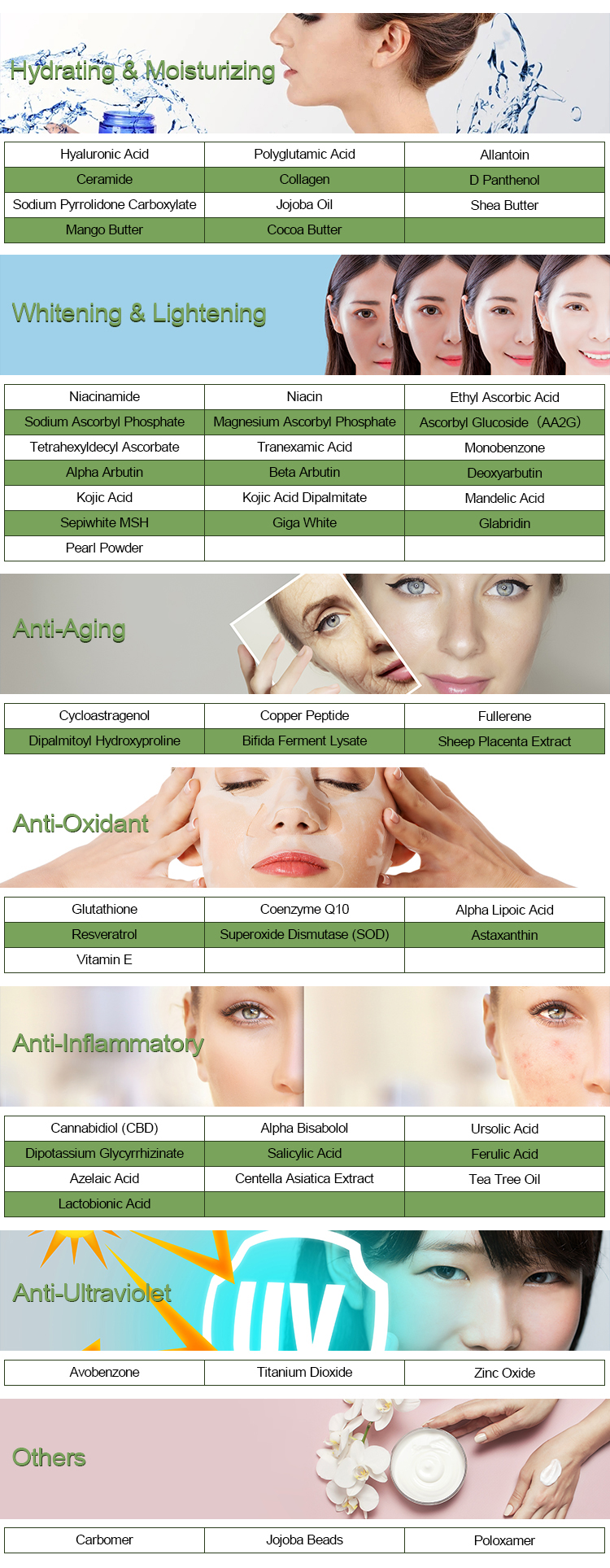
6. Future Trends
- Genetically Engineered Silk: Advances in biotechnology have allowed for the production of silk fibroin using recombinant DNA techniques. This could reduce the dependence on silkworms and increase production efficiency.
- Synthetic Biology: Through synthetic biology, researchers are looking to produce silk fibroin in microbial systems, which could further lower costs and improve scalability.
- Smart Materials: Researchers are working on silk fibroin-based materials that can respond to external stimuli (e.g., pH, temperature) for use in responsive and adaptive materials in medicine and electronics.
The future of silk fibroin is bright, with increasing applications in advanced biomedical fields, sustainable materials, and smart textiles.