Magnesium Ascorbyl Phosphate (MAP) is a water-soluble derivative of vitamin C (ascorbic acid) that is commonly used in skincare products due to its antioxidant and skin-brightening properties. The basic component of Magnesium Ascorbyl Phosphate is a combination of ascorbic acid (vitamin C) and magnesium.
Here’s a breakdown of the basic components:
Ascorbic Acid: This is the active form of vitamin C, which is well-known for its antioxidant properties. Vitamin C helps protect the skin from damage caused by free radicals and UV radiation. It also promotes collagen production and can help reduce the appearance of fine lines and wrinkles.
Magnesium: In Magnesium Ascorbyl Phosphate, magnesium is added to stabilize the ascorbic acid and make it more suitable for use in skincare products. This stabilization helps prevent the rapid degradation of vitamin C when exposed to air and light, which can occur with pure ascorbic acid.
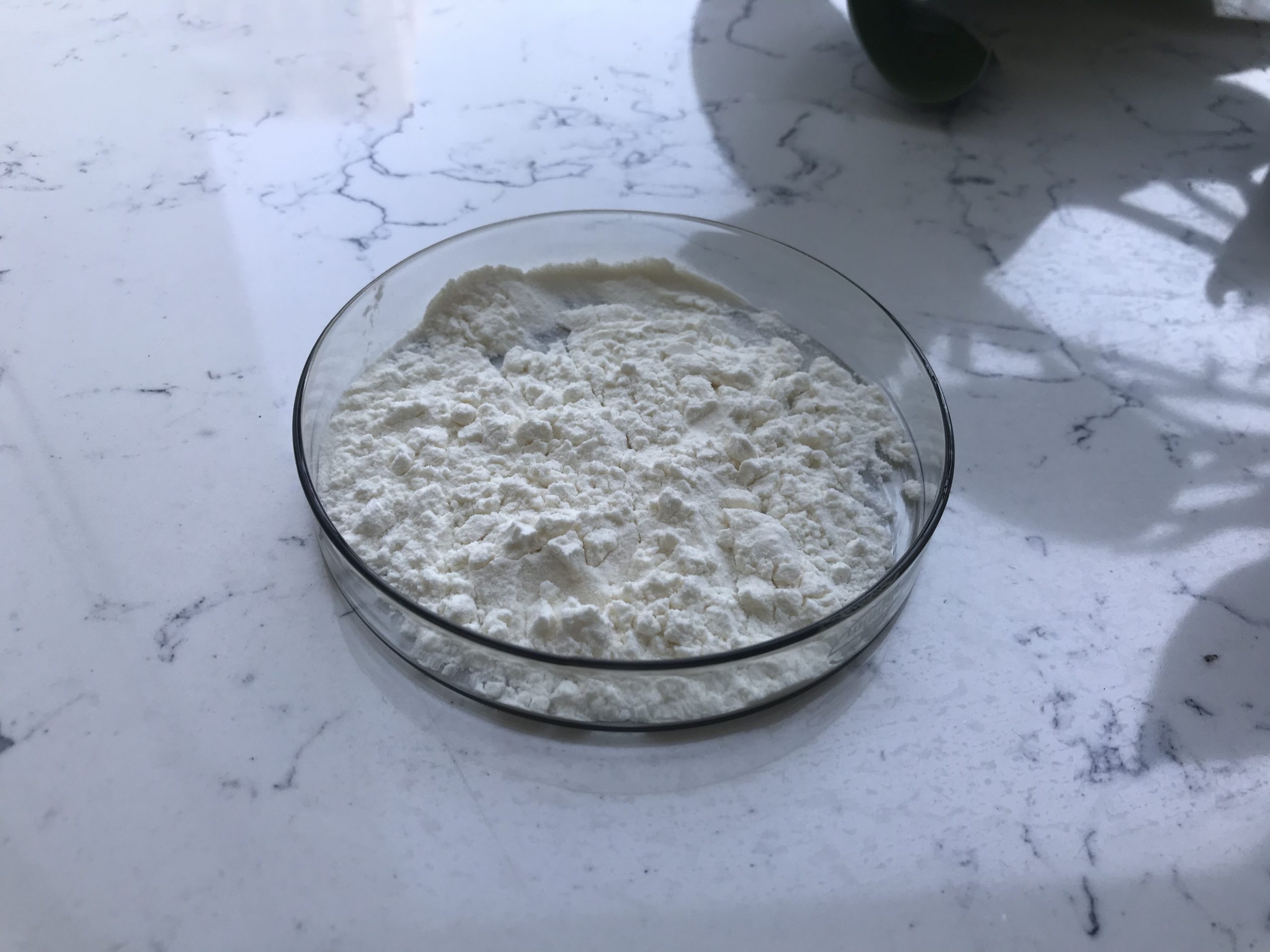
Together, these components create Magnesium Ascorbyl Phosphate, a form of vitamin C that can be easily absorbed by the skin and is less likely to cause skin irritation compared to pure ascorbic acid. It is often included in skincare products like serums and creams to provide the skin with the benefits of vitamin C, such as brightening and protecting against oxidative damage.
The production technology of Magnesium Ascorbyl Phosphate
Magnesium Ascorbyl Phosphate (MAP) is a water-soluble derivative of Vitamin C (ascorbic acid) that is commonly used in cosmetics and skincare products for its antioxidant and skin-brightening properties. It is less sensitive to oxidation than pure ascorbic acid, making it a stable option for topical applications. The production technology of MAP involves several steps:
1.Starting Materials: The primary starting material for Magnesium Ascorbyl Phosphate production is ascorbic acid, which can be obtained from various sources, including corn, citrus fruits, or synthesized chemically. The ascorbic acid is the core component that will be modified to create Magnesium Ascorbyl Phosphate.
2.Esterification: To create Magnesium Ascorbyl Phosphate, ascorbic acid undergoes esterification. This involves reacting it with phosphoric acid and magnesium oxide or magnesium hydroxide. The reaction takes place under controlled conditions, usually at a specific temperature and pH.
3.Neutralization: After esterification, the reaction mixture is typically neutralized using an alkali (such as sodium hydroxide or potassium hydroxide) to achieve the desired pH level. This step helps stabilize the Magnesium Ascorbyl Phosphate compound.
4.Purification: The crude Magnesium Ascorbyl Phosphate product obtained from the previous steps may contain impurities. Purification is essential to obtain a high-quality Magnesium Ascorbyl Phosphate product. Various methods, such as filtration or crystallization, can be used to remove impurities and isolate the pure Magnesium Ascorbyl Phosphate compound.
5.Drying: The purified Magnesium Ascorbyl Phosphate is often in the form of a wet cake or paste. It needs to be dried to obtain a powder or granular form, which is more suitable for cosmetic and skincare product formulations.
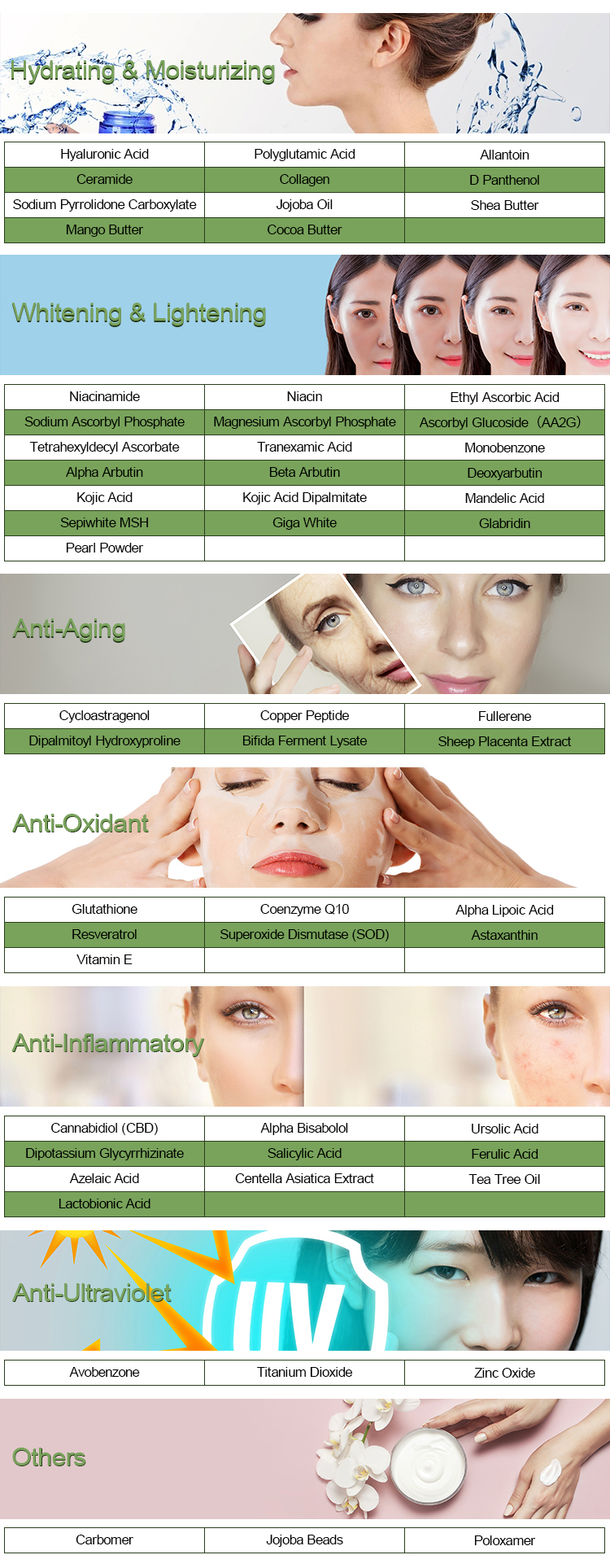
6.Quality Control: Throughout the production process, quality control measures are essential to ensure that the Magnesium Ascorbyl Phosphate product meets specific purity, pH, and stability criteria. Various analytical techniques, such as high-performance liquid chromatography (HPLC), are used to assess the quality of the final product.
7.Packaging: Once the Magnesium Ascorbyl Phosphate powder is obtained and tested for quality, it is typically packaged in airtight containers to prevent moisture and air from degrading the compound. Proper packaging helps maintain the stability of Magnesium Ascorbyl Phosphate.
8.Labeling and Documentation: The final step involves labeling the product with relevant information, including the chemical name, CAS number, batch number, and other regulatory requirements. Detailed documentation of the production process is maintained for quality control and regulatory compliance purposes.
It’s important to note that the production of Magnesium Ascorbyl Phosphate should be carried out in accordance with industry regulations and quality standards to ensure the safety and effectiveness of the compound in cosmetic and skincare products. Manufacturers must also adhere to good manufacturing practices (GMP) and maintain appropriate quality control measures throughout the production process.